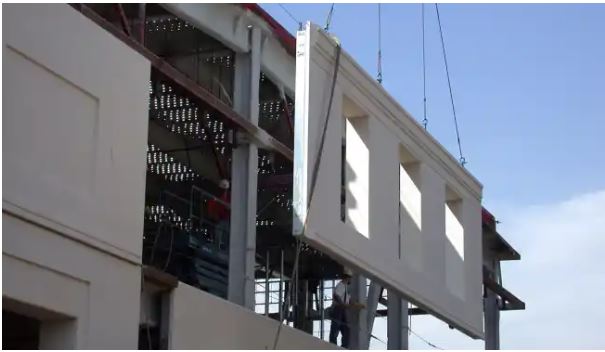
Introduction:
Over the past two decades, the construction industry in Uganda has witnessed consistent growth, contributing over 13% to the nation’s GDP, even in the face of rising inflation. This industry serves as a significant indicator of a nation’s economic health, reflecting the growth of various other sectors. Recent data from the Bank of Uganda (BOU, 2023) shows a positive trend, with GDP from Construction in Uganda increasing to 2226.50 UGX Billion in the first quarter of 2023. Amidst these developments, the construction sector has been undergoing a transformative shift, with the emergence of Precast Flat Panel Construction Modules as a modern, efficient, and cost-effective construction method.
The Evolution of Construction
The roots of construction trace back to ancient times when humans constructed shelters using readily available materials like wood, mud, and stone. As civilizations advanced, so did construction techniques, with copper, bronze, and eventually iron becoming predominant. The 19th and 20th centuries marked industrial revolutions that significantly improved construction quality and speed. Today, we have reached an era where technology enables the rapid construction of complex structures, with a growing emphasis on sustainability.
In Uganda, the construction industry has evolved from traditional brick and mortar to embrace the Precast Flat Panel System. This innovative technique involves manufacturing flat concrete panels for walls, floors, and roofs in a factory and then assembling them on-site. An excellent example of this method in action is the construction of BAAJ Apartments on Mutungo Hill. The panels are produced at facilities like the D3N9 factory in Namanve and then transported to the construction site for assembly. The process involves several key steps:
Site Prefabrication: Setting up a dedicated factory near the construction site to produce precast panels efficiently. Quality control measures should include complete testing facilities to ensure adherence to prescribed quality standards.
Moulds: Precast concrete components are typically made using steel moulds for their durability. However, plywood formwork may be used for smaller quantities of precast elements to reduce costs.
Transportation: Panels are carefully loaded onto trailers and securely fastened to prevent damage during transit. The stacking area at the construction site must be level and sturdy.
Precast Installation and Erection: Panels are lifted into place using cranes and then grouted after final adjustments.
Benefits of Precast Flat Panel Construction: This construction technology offers several advantages:
- Time Savings: Significantly reduces construction time, often by more than 50%, compared to traditional methods.
- Cost-Effective: Simplified processes increase productivity, quality, and safety, leading to cost reductions.
- Durability: Precast concrete structures have a longer service life and require minimal maintenance.
- Temperature Control: Maintains comfortable room temperatures in various climates.
- Quality Assurance: Each panel undergoes quality checks, is barcoded, and is delivered “just in time” for the project.
Challenges Associated with Precast Construction: While this method offers numerous benefits, it also presents some challenges:
- High Initial Investment: Establishing a precast concrete plant requires heavy machinery and a substantial initial investment.
- Handling Difficulties: Poor handling during transportation can result in panel damage.
- Modification Challenges: Structural modifications can be complex and affect overall stability.
- Connection Sensitivity: Faulty connections may lead to issues such as water leakage and sound insulation problems.
Conclusion
In conclusion, to keep pace with evolving construction trends, it is crucial to embrace new technologies such as Precast Flat Panel Construction Modules. This innovative approach offers faster construction times, increased durability, and overall cost savings, making it a promising solution for Uganda’s growing construction needs. However, it’s essential to address the associated challenges effectively to maximize the benefits of this construction method.